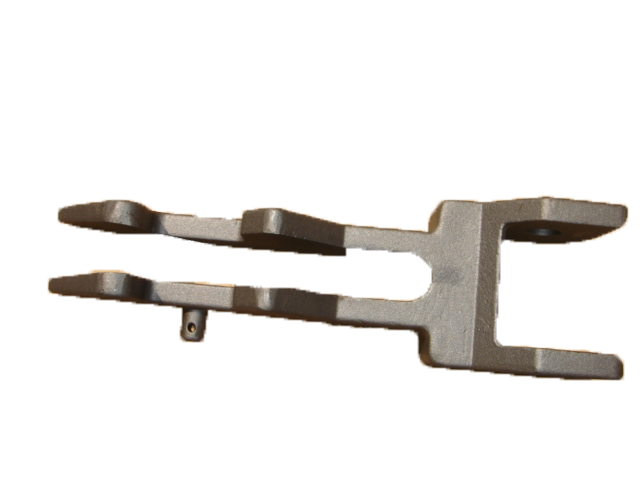
A Brief Introduction to the Precision Casting Process
- Start making the mold according to the requirements of the user's drawings. The mold is divided into upper and lower concave molds, which are completed by milling, turning, planing, etc. The shape of the pit of the mold should be consistent with the half of the product. Because wax molds are generally mainly used for industrial wax pressing, we need to choose aluminum alloy materials with low hardness, low requirements, low price, slightly lighter weight and low melting point as molds.
- After selecting the aluminum alloy material, we can use this aluminum alloy to produce a large number of industrial wax solid models. Under normal circumstances, an industrial wax solid mold can only produce one rough product.
- After the wax model is completed, it is necessary to modify the margin around the wax model. After removing the excess on the surface, it is necessary to stick a single wax model to the prepared die head one by one.
- Apply industrial glue to the die head that we have glued multiple wax molds, and then evenly spray a layer of refractory and high temperature resistant silica sand. The sand particles are very small and fine, which can ensure that the surface of the final blank is smooth.
- Then put the wax mold in the factory where we have set the room temperature for natural air drying, but it cannot affect the shape change of the internal wax mold. The natural single air drying time depends on the internal complexity of the mold. Generally speaking, the drying time is 5- 8 hours or so.
- After the wax mold is air-dried, it is necessary to continue to apply another layer of industrial glue on the surface of the wax mold, and spray a second layer of sand. The sand of the second layer is larger and coarser than the sand of the first layer. After touching the second layer of sand, it is the same as the first layer, and it is naturally air-dried.
- After the sand on the second layer is naturally air-dried, the third layer, the fourth layer, and the fifth layer of sandblasting should be carried out in sequence. Sandblasting requirements: We need to adjust the corresponding sandblasting times according to the surface requirements and volume of the product. Under normal circumstances, the number of sandblasting will be about 3-7 times. The particle size of each blasting is also different, the sand in each process is thicker than the previous one, and the drying time is also different. Generally, the sanding cycle of a complete wax mold may be about 3 to 4 days.
Determination method of pouring surface of precision casting
The position of the casting in the mold during pouring affects the quality, dimensional accuracy and difficulty of the casting process.
Selection principle of pouring position:
- The important processing surface or main processing surface of the precision casting is facing down or on the side: when pouring, the gas, slag and sand in the mold will float up in the molten metal, which may cause pores, slag inclusions, etc. to appear in the upper part of the casting. Defects such as trachoma, and the possibility of defects in the lower part of the casting, the structure is denser.
The pouring position of the machine bed should face the guide rail down to ensure the quality of this important working surface. The quality requirements of the circumferential surface are relatively high, and the vertical pouring scheme can make the circumferential surface on the side, and the quality is uniform.
- The large plane of the precision casting is poured downward or inclined: due to the strong thermal radiation of the hot metal liquid to the upper part of the mold during pouring, the top sand mold will expand and arch or even crack, causing sand inclusions, sand holes, etc. on the large plane. defect. The production casting defects of the large plane can be avoided by the method of casting the large plane downward or adopting the inclined pouring method.
- The thin-walled part of the precision casting faces downwards, stands sideways or is inclined: in order to prevent the thin-walled parts of the castings from being cold and unable to be poured, the thin-walled part with a larger area should be placed at the lower part of the casting, or placed on the side wall or tilted position.
- The thick part of the precision casting should be placed on the top or on the side of the parting surface. The main purpose is to facilitate the placement of the riser in the thick part for feeding.
Conclusion
For more information about investment and precision casting,silica sol precision casting,design precision castings, we are glad to answer for you.